Practical Six Sigma
By PJ Stevens
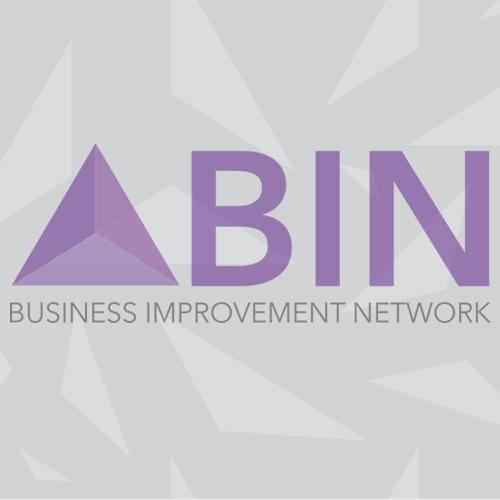
What is Six Sigma?
Six Sigma is a set of techniques and tools developed in the 1980s by two engineers, Bill Smith and Mikel J. Harry, who introduced the practices to the Motorola company for which they worked at the time.
What are the Six Sigma principles?
The objective of Six Sigma is to improve the quality of products made using a particular process, by eliminating factors that cause defects, and reducing variations in production methods that can lead to variations in quality. This is achieved with a series of quality management tools that focus on gathering and analysing statistical and empirical data. Another key aspect of Six Sigma is a focus on training key employees at all levels of the organisation as experts in Six Sigma methods. Working together, these employees can then ensure that at every stage of a given process, Six Sigma principles are being applied and perfected.
With Six Sigma, the focus is very heavily on data, both in analysing processes and setting objectives. Six Sigma strives towards developing near-perfect processes, with “near-perfect” defined as six standard deviations between the mean and the nearest specification limit. In fact, this is where this process improvement method gets its name—sigma is the symbol used to denote a standard deviation on a distribution curve. Six Sigma is literally near-perfection, as an error-rate that falls six standard deviations outside the mean is a rate of 2 in a billion.
What is the Six Sigma method?
Six Sigma employs a number of different strategies for improving business processes. One of the most widely-used is DMAIC (duh-may-ick), a series of five steps in a cyclical improvement process.
1. Define: In this first step, a number of parameters are defined. The target customer group, their needs and expectations; the process under investigation; and the start and end point and boundaries of the project.
2. Measure: Here, data is collected in order to measure the key performance indicators of the business process.
3. Analyse: The data previously collected is analysed and process-mapped to determine what gaps exist between current and ideal performance levels, and where the process needs improvement. When these opportunities for improvement are defined, they can be ranked and prioritised in terms of the potential value they can add to the process.
4. Improve: This stage is about implementing improvements—creating solutions for the problems identified in stage 3, and rolling them out. This might be done in multiple stages, or all at once.
5. Control: The organisation’s systems and structures need to support the changes that have been made, in order to ensure that they are sustainable in the long term. This stage might include implementing incentives for achieving certain goals, providing training for staff, or employing new staff members, depending on what’s needed.
Another process often associated with Six Sigma is the Plan, Do, Check, Act cycle, a continuous improvement model developed by W. Edward Deming. In this model, changes are first made on a small scale, and often includes testing a number of alternatives against one another. After data analysis to determine the most effective option, the new and improved process is rolled out across the entire company.
What are the results produced employing Six Sigma?
The results that successful implementation of Six Sigma can produce are fairly well-known, thanks to the high profile of the first usages of the method in Motorola, Allied Signal, General Electric, Honeywell, and Ford, between 1986 and 2000. Each company saved billions in the first years of implementation, amounting to 1.2% to 4.5% of revenue in savings. BPI experts iSixSigma note that while this doesn’t make Six Sigma a “get rich quick” scheme, it’s a significant result that impacts any company’s bottom line.
About the author
PJ Stevens is an expert in organisational change, performance and improvement, with 20 years experience. He is chair of the business improvement network.
Enjoyed reading these articles?
Have you got something you can share with the Network. Why not submit an article