Continuous Improvement
By PJ Stevens
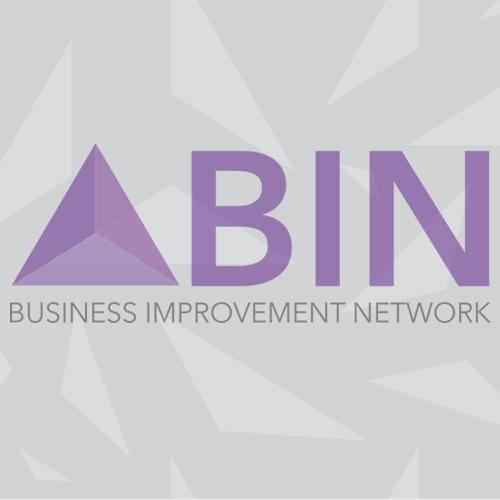
Business process improvement seeks to make organisations more efficient and profitable by reducing redundancy and waste in the various processes that allow them to operate. Continuous improvement recognises that the process of making improvements is one that is never complete.
What is Continuous Improvement?
Continuous improvement refers to an ongoing process of improving an organisation's profitability by making improvements to business processes, services, and products. The changes that are made can be incremental—made gradually over time—or breakthrough improvements that are implemented all at once.
What are some Models of continuous improvement?
The PDCA cycle
While there are multiple models for the continuous improvement process, one of the most commonly-used is the PDCA cycle developed by W. Edward Deming, an early thought leader in the field.
PDCA is an acronym that stands for Plan, Do, Check, Action. Within the PDCA cycle, these four steps are repeated more-or-less continuously over time, resulting in long-term incremental improvement and learning for a given process, product, or service.
Within each stage, there are specific objectives to meet and tasks to perform before moving to the next.
1.Plan: This stage is about identifying opportunities for positive change, by analysing current processes, products, and services, and looking at various ways in which improvements might be made. This is also the time to look at possible barriers to change, and different ways in which changes can be implemented.
2.Do: In this stage, it’s time to test one or more alternative changes. This can be thought of as similar to an A/B test, where two or more iterations are tested against one another. For instance, testing different sales or display methods in a retail store, or different production methods in a manufacturing plant.
3.Check: Here is where the data gained from stage 2 are analysed and assessed. Has the trial produced actionable results—meaning, is there enough information to proceed to stage 4? Alternatively, does the trial need to be extended, revised, or ended altogether?
4.Act: The change is made and implemented on a wider scale, e.g. within the entire organisation.
Under the PDCA cycle, of course, the process does not end here; rather, from stage 4 the process starts anew at stage 1, with a new round of analysis.
Commercial models of continuous improvement
Commercially-developed models include Lean, Six Sigma, and Total Quality Management. Each of these uses different proprietary methods that put the emphasis on involving employees in improvement processes, and quantitative analysis and developing systems to reduce variation and improve quality in processes, products, and services.
Potential benefits of continuous improvement: case study
Continuous improvement methods have huge potential for effecting positive change within an organisation. One case study of note is that of Leyland Trucks, a Lancashire manufacturer with plants in the UK, The Netherlands, and Belgium. The company hoped to increase its market share from 15% to 20% via increased production capacity and continuous improvement over a period of time. To do this, the company adopted principles of Kaizen, a continuous improvement method developed by Japanese management consultant Masaaki Imai, within a Six Sigma framework. Using these methods, Leyland Trucks implemented an innovative production line utilizing robots on a moving conveyor, using key performance indicators such as productivity, quality, financials, healthy and safety, and on-time performance.
One practice that enabled Leyland Trucks to succeed was its company culture, which involved employees at all levels of the company in making key decisions, and empowered employees to take responsibility, make decisions, and be innovative.
The results were unequivocal: multi-million pound savings, 10% fewer mechanical defects, 45% fewer reportable injuries, and an on-time delivery rate of more than 95%, demonstrating clearly the benefit of adopting continuous improvement practices.
About the author
PJ Stevens is an expert in organisational change, performance and improvement, with 20 years experience. He is chair of the business improvement network.
Enjoyed reading these articles?
Have you got something you can share with the Network. Why not submit an article