Lean
By PJ Stevens
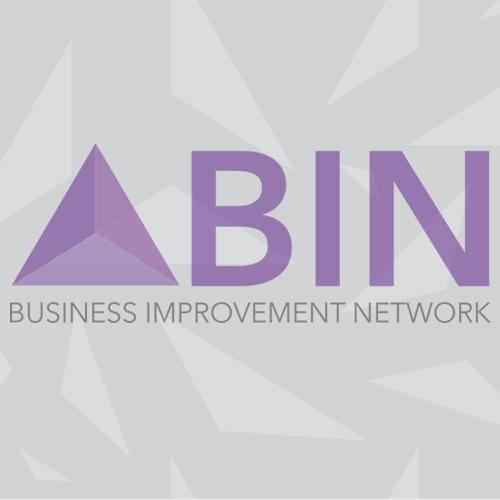
Lean is a method of implementing continuous improvement within an organisation, with a focus on reducing waste and maximising customer value. According to the Lean Enterprises Institute, the ultimate goal for a lean organisation is to provide 'perfect value' by implementing zero-waste creation processes.
The term 'lean' was first used in this way during the late 1980s, by a research team at MIT. Headed by James Womack, Ph.D., the research group—the International Motor Vehicle Programme—used the term to describe Toyota’s production methods. Lean was introduced to the world in Womack’s book The Machine that Changed the World, where the author described how lean manufacturing principles had boosted Toyota’s profitability and reputation.
What are the principles of Lean management?
The Lean Enterprises Institute, founded by James Womack and Dan Jones, has developed a five-step process that's intended as a guide for implementing Lean techniques within an organisation.
1. Identify value: From the customer's point of view, meaning, what value will a customer gain when Lean techniques are implemented?
2. Map the value stream: What steps are involved in the value stream for a given product or product family? Which of those steps are needed in order to create more value? If any steps don't add value, can they be eliminated?
3. Create flow: Create a logical sequence of value-creating steps that ensure products are available to customers. This stage is about developing a process that's predictable, with as little variation as possible.
4. Establish pull: In a 'pull' system products are manufactured as needed rather than well in advance, reducing waste while ensuring that customer demand is met.
5. Seek perfection: Repeat the process to continuously refine the flow, improve value, and reduce waste.
Is Lean only for manufacturing methods?
Although the Lean principles are ostensibly geared towards organisations involved in manufacturing, they can be applied to all kinds of organisations and business processes. According to the LEI, Lean is "a way of thinking and acting for an entire organisation," and the principles of Lean are much more universal than they appear at first glance. For instance, creating customer value and reducing waste—the core concepts of Lean management—can be applied to any kind of business, in any industry.
What is the Lean transformation?
The process by which an organisation switches from old business methods to new ones guided by Lean principles is called Lean transformation. Here, The Lean Enterprise Institute suggests three fundamental issues that should be essential parts of the process.
Purpose: The organisation’s ultimate objective in implementing Lean principles is to improve profitability. What customer problems can the organisation solve in order to do this?
Process: How will the organisation assess its major value streams to ensure that each stream, and the steps involved, create value?
People: How will the organisation evaluate each value stream, and ensure that everyone involved in a given value stream is actively engaged in improving it?
A Lean implementation case study
While the principles of Lean management can be most easily—and obviously—applied to manufacturing, the following case study demonstrates how well they apply in a more universal sense, for businesses of all sizes. This implementation of Lean methods was orchestrated by Continental Design & Engineering, with the objective of streamlining the accounting department of a medium-sized business. For this organisation, the main issue was that the accounting department was slow to deliver monthly financial data to key executives, missing the 8-day deadline up to one-third of the time.
A value stream map of the accounting department’s processes showed that the process flow worked in sequence, with each person involved completing part of the work before handing off to the next. As a result, if any single person in the chain was delayed, the entire department missed their deadline. The solution was simple but effective: the entire process was overhauled so that several phases of the work could be completed in parallel, with stellar results. The new-look process was completed on time 100% of the time, in 5 days rather than 8, with the result that the company’s executives had that essential data on hand much more quickly than before.
About the author
PJ Stevens is an expert in organisational change, performance and improvement, with 20 years experience. He is chair of the business improvement network.
Enjoyed reading these articles?
Have you got something you can share with the Network. Why not submit an article